Traditional Handcrafted Bronze
Article and Photographs Coutesy of Dinsdale Petch
Running Dog Bronze
www.dinsdalepetch.co.uk
Adam Binder and Dinsdale Petch are working together to produce Adam's new Bronze Sculptures and Miniatures. Mr. Petch has provided the information and photographs below to explain how bronze sculptures are made. We thank him for allowing us to share with you the details of this complicated process.
Traditional bronze is an alloy of tin and
copper. Both these metals are inherently
soft, but when mixed, or alloyed, they
become much harder.
Nowadays, the same result is achieved by
mixing silicon with the copper. This addition creates a very fluid alloy which captures the finest details.
The Original 'Pattern'
The 'pattern' or the original piece to be
copied can be of virtually any subject, an
artist's original sculpture, a piece of fruit
or an old sculpture.
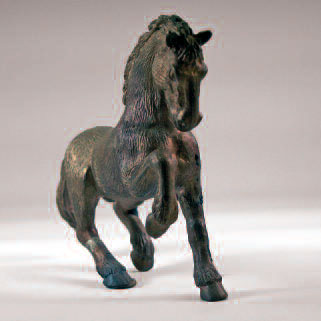
Hand chased bronze master pattern
The Rubber Mould
Using a very high quality silicon polymer,
the original pattern is covered. This then
forms the master for as many copies as
may be needed. Great care is taken to
copy the tiniest details.
The Wax Pattern
A pattern is prepared in wax, using the
rubber mould. The quality of the wax
determines the degree of detail that can
be reproduced. Again different grades
of wax may be needed even within the
same piece.
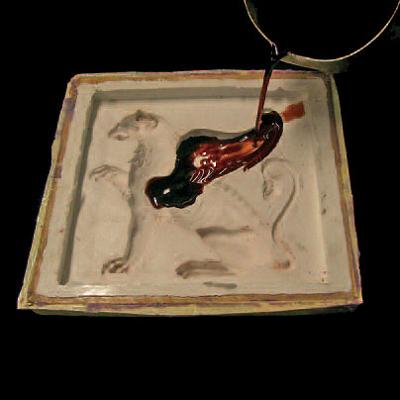
Hot wax being poured into open rubber mould
The image (above) shows a simple open mould made up of a rubber membrane supported by a composite case. Sculptures like Adam's, that are designed to be viewed from all angles, require rubber moulds made up of interlocking pieces to allow the delicate wax castings, complete with tails and tips of ears, to be removed from the mould without breaking.
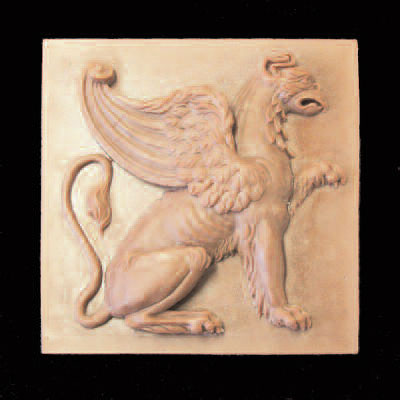
Wax plaque on removal from mould
Wax Fettling
Any imperfections within the wax are
repaired and any areas where the wax
has ‘flashed’ are cleaned.
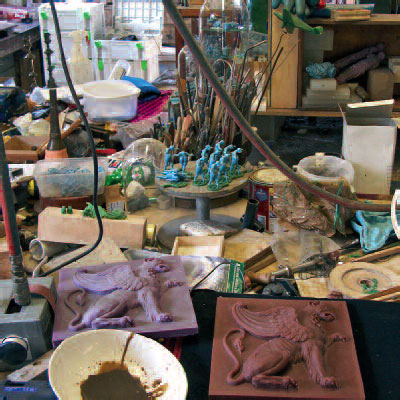
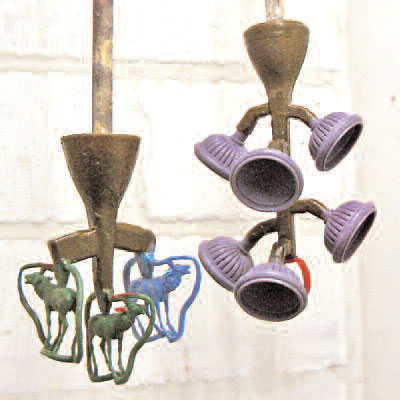
Wax trees awaiting dipping
Wax Tree
The wax patterns are 'gated', ie provided
with a cylinder of wax through which the
molten metal will enter the mould.
When it is ready the finished object often
resembles a tree.
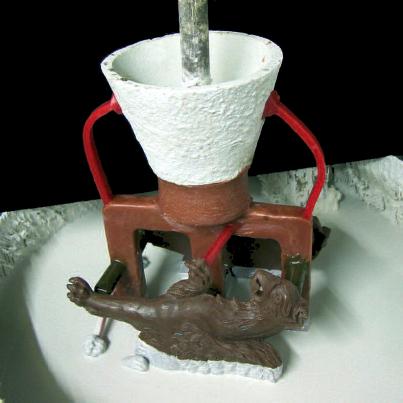
Wax tree being dipped into first coat of ceramic slurry
A Ceramic Shell
The original ceramic coating or shell is
now carefully created, built up by dipping
and re-dipping the wax tree alternately
into a mineral ceramic slurry then into graded
ceramic sands and grits.
Several layers are built up - each being
allowed to dry thoroughly between dips.
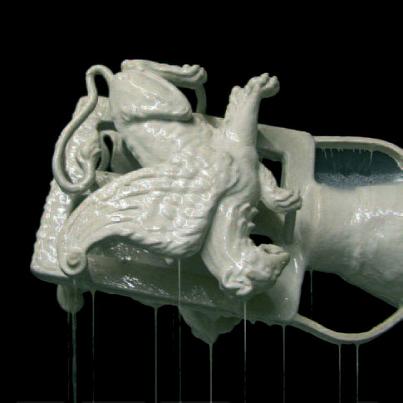
Wax tree undergoing first ceramic dip
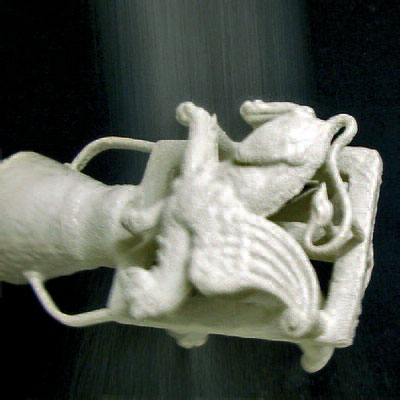
Raining ceramic grit and sand onto wet slurry on wax tree

Dewaxing
Once it is dry, the ceramic shell is placed
in a kiln to melt the wax. The wax is
collected and re-used for future wax
trees. The ceramic shell is now hollow,
the vacant space inside representing the
original pattern.
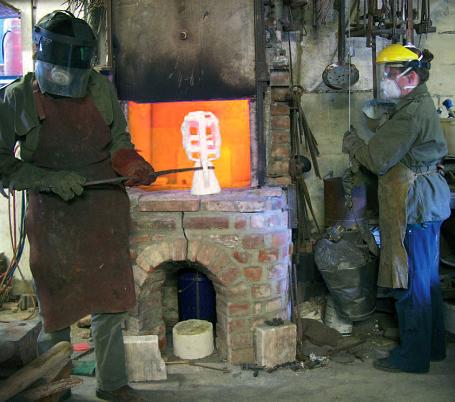
Hot mould being removed from burn out kiln ready to have molten bronze poured into it
Melting the Bronze
The bronze is melted, an alloy of copper
and silicon with traces of other metals.
The entire crucible needs to be at exactly
the right temperature and fluidity when
the liquid is poured.
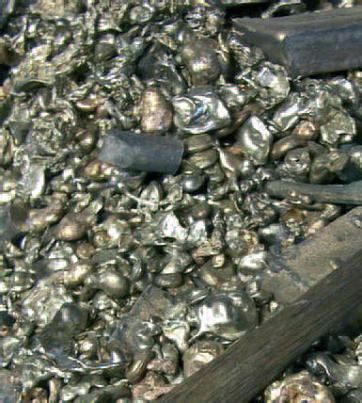
Raw bronze grain before being melted in a crucible in the furnace
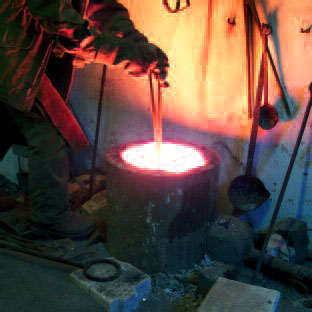
Removing crucible from furnace
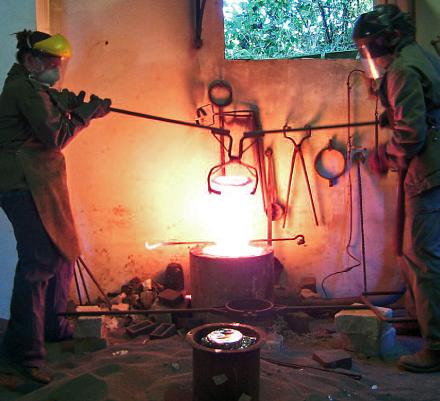
Lifting large crucible of bronze from furnace at 1100 degrees C
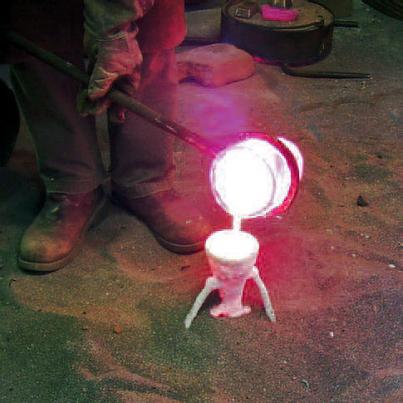
Pouring bronze into a small ceramic mould buried in sand
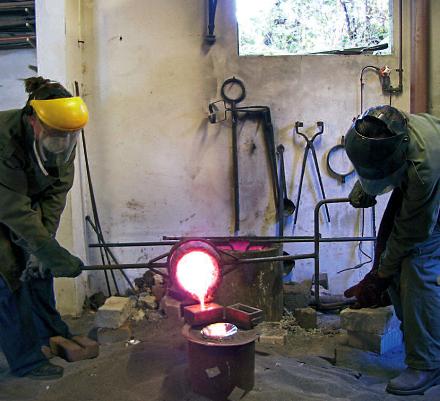
Pouring spare bronze into ingot moulds for re-use
Removing the Shell
About half an hour after 'the pour', the
shell can be removed to reveal the
bronze. The bronze itself has contracted
slightly, thus detailed areas tend to grip
the ceramic shell.
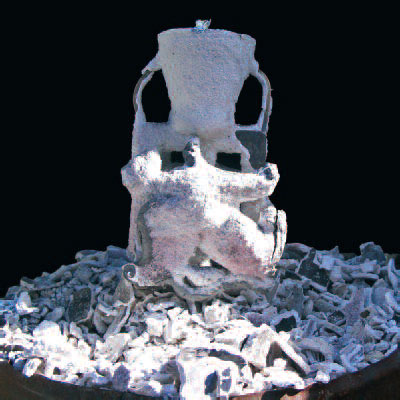
Destructive removal of ceramic mould from fresh cast bronze
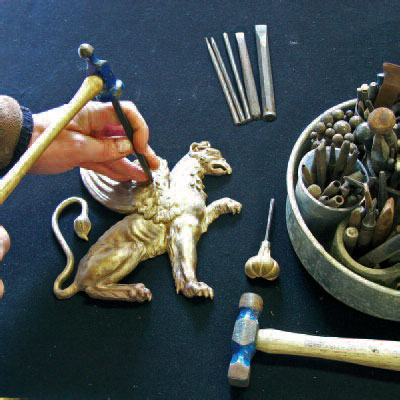
Many hours later the final touches remove the slightest imperfections prior to patination
Finishing the Bronze
Where the wax tree had branches, the
piece now has bronze branches which
need to be removed, the cut faces
smoothed and, if necessary, chased to
match the surrounding texture.
Patinating the Bronze
The final touches involve polishing or
patinating, which can produce a variety of
finishes. There are many secret recipes
involved to patinate the bronze.
The art of the patineur, involves sensitivity
to the subject and traditional patineurs
would never reveal their recipes. Much
research, involving the most unlikely
processes has been carried out to
produce the richness of variety available
to the contemporary bronze artist. It is important to remember patination is not paint - the rich colors are achieved by the use of many different chemical compounds that bring about 'rapid weathering' of the bronze surface. Once the desired colour has been reached, the surface is sealed with a durable lacquer prior to waxing.
Mrs. Petch said that during the development of Adam's bronze sculptures for his Exhibition, Adam was a regular visitor to the foundry. Both Mr. Petch and Adam experimented with different recipes in the patination stage to get the exciting finishes for his sculptures!
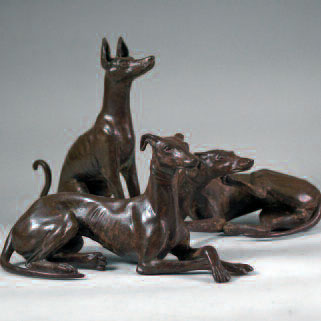
Finished Patinated bronzes (classic brown patina)
Many collectors of Adam's earlier work are familiar with the making of the marble/resin pieces. Mr. Petch summarized the similarities and differences between these two processes: "The rubber moulds used in the wax making stage at the beginning of the bronze process are the same as those used for resin production. Instead of resin, we pour in molten wax which, once set, is removed and dipped repeatedly in the ceramic slurry which, once set, forms a tough ceramic mould capable of receiving molten metal. The wax is melted away and replaced by the molten bronze. Once cool, the ceramic mould itself is destroyed to recover the raw bronze sculpture.
In order to produce each individual bronze, we need one wax and one ceramic mould - both of which are destroyed in processing." - Dinsdale Petch
To see original PDF file, click here.
Dinsdale Petch
Running Dog Bronze
www.dinsdalepetch.co.uk
4 The Square, East Buckland
Barnstaple, North Devon EX32 0TA
Tel: 01598 760558